Electrostatic Powder Coating
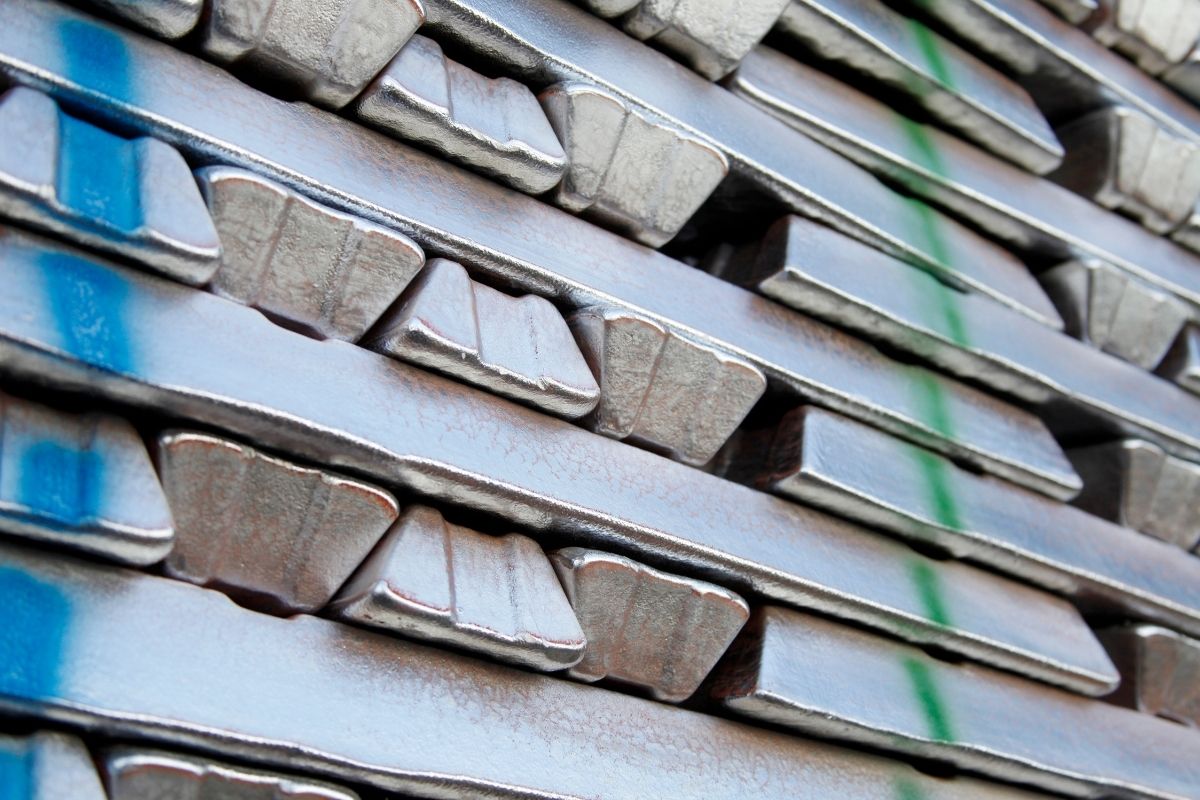
Aluminum is a preferred material in many sectors with its lightness, durability and aesthetic appearance. However, surface treatments are needed to protect it against external factors and maintain its aesthetic appearance. In this context, electrostatic powder coating stands out as one of the most effective and popular methods for protecting aluminum surfaces. So, what is electrostatic powder coating and how does it provide long-lasting protection on aluminum surfaces? In this article, we will answer these questions.
What is Electrostatic Powder Coating?
Electrostatic powder coating is the process of coating metal surfaces, especially aluminum, with electrostatically charged powder paint. The powder paint is adhered to the metal surface as fine particles by means of an electrostatic field. This process ensures that the paint adheres homogeneously to the surface. After the powder coating is applied, the surface is baked in a high temperature oven, where the paint melts and adheres permanently to the surface of the aluminum.
Advantages of Powder Coating
Electrostatic powder coating offers many advantages on aluminum surfaces. Here are the prominent benefits of this method:
- Durability: Powder coating gives aluminum surfaces excellent mechanical durability. It provides high resistance to scratches, impacts and abrasion.
- Corrosion Resistance: Powder coated aluminum provides excellent protection against moisture, water, salt and chemicals. This is especially important in outdoor applications.
- Long Life: Powder coating is much more durable than traditional liquid paints and retains its color and gloss for many years. This reduces maintenance costs for aluminum surfaces.
- Environmentally Friendly: Powder coating is solvent-free and does not emit volatile organic compounds (VOC). Therefore, it is known as an environmentally friendly coating method.
Electrostatic Powder Coating Process
The powder coating process consists of several steps and each step determines the quality of the result:
- Surface Preparation: Aluminum surfaces should be cleaned and degreased. This is important for the paint to adhere well to the surface. Cleaning is usually done with chemical solutions or mechanical methods.
- Powder Coating Application: The cleaned aluminum surface is coated with powder paint. Since the paint is electrostatically charged, it forms a homogeneous layer on the metal surface.
- Baking: Powder coated aluminum parts are baked in high temperature ovens. This process ensures that the paint melts and permanently adheres to the aluminum surface. Baking time and temperature are adjusted according to the type of powder coating used.
- Cooling and Quality Control: After firing, the painted parts are cooled and subjected to quality control. At this stage, the homogeneity of the paint, color consistency and possible defects on the surface are examined.
Areas of Use
Electrostatic powder coating is widely preferred in many different areas where aluminum is used:
- Exterior Cladding: Provides long-lasting protection in exterior applications such as aluminum facade panels, doors and window profiles.
- Furniture and Decoration: It offers an aesthetic and durable coating on aluminum furniture and decoration products used indoors.
- Automotive Industry: It is used in aluminum parts of vehicles to increase durability and give an aesthetic appearance.
- Electronic Devices: It is used as both a protective and aesthetic coating on electronic device cases made of aluminum.